Imagine increasing your factory throughput by up to 30% just by upgrading your welding process. Industrial laser welding is unlocking that level of efficiency for manufacturers worldwide, delivering higher quality, speed, and cost-effectiveness. In this detailed guide, you'll learn how embracing this game-changing technology can help you outpace your competitors and achieve operational excellence.
Why Industrial Laser Welding is Revolutionizing Modern Manufacturing
- Did you know industrial laser welding can boost production efficiency by up to 30% compared to conventional welding machines? This article explores why this technology is changing the face of manufacturing, enhancing speed, precision, and cost-effectiveness.
Manufacturers across the globe are making the switch to industrial laser welding for its unparalleled efficiency and innovation. With the advent of fiber laser technology, welders can achieve faster production times, greater consistency, and reduced operational costs . For example, automotive plants have reported significantly higher throughput and tighter quality control after integrating laser welding systems into their assembly lines. Aerospace and electronics sectors also benefit from micro-precise welds and minimal rework, cutting down waste and boosting profit margins.
The difference lies in the laser beam's pinpoint focus , enabling strong welds with minimal heat impact on materials like stainless steel, titanium, and aluminum . Unlike MIG or TIG welding, laser welders can automate complex tasks, making them perfect for large volume production. The bottom line? Laser welding machines don't just weld parts, they refine entire manufacturing workflows for a more competitive edge.
What You'll Learn About Industrial Laser Welding
- • Key benefits of industrial laser welding
- • Comparison with traditional welding techniques
- • How laser welding machines deliver higher quality welds
- • Factors to evaluate when choosing a laser welder for your operations
- • Real-world examples and industry applications
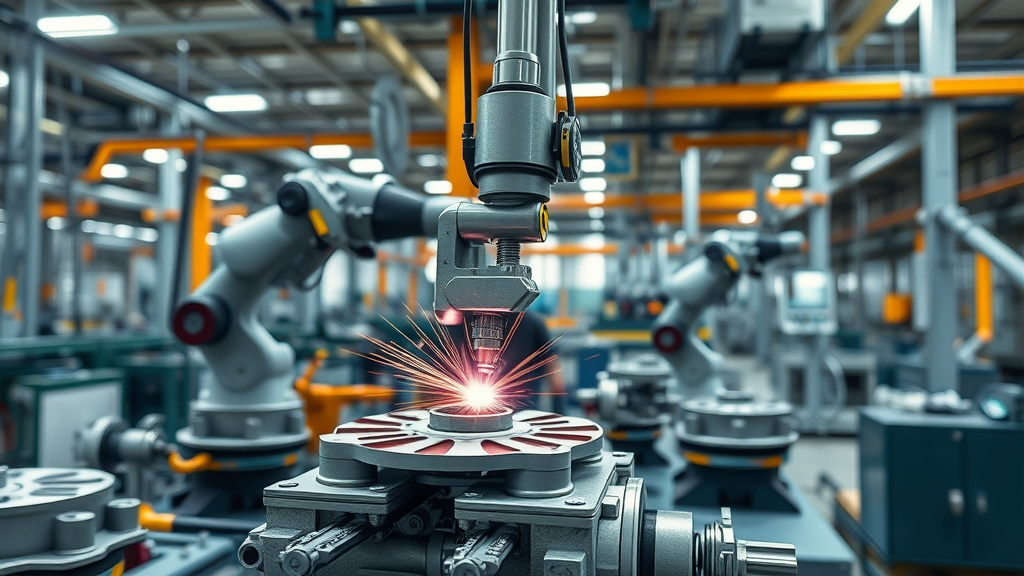
Understanding Industrial Laser Welding: Core Principles & Processes
At its core, industrial laser welding fuses two or more metal components together through an intensely focused laser beam. The technology is powered predominantly by fiber lasers , a type of laser that channels energy through a fiber optic cable, delivering high-intensity light directly to the target material. This means exceptional melting precision, reduced risk of warping, and minimal post-processing.
There are several welding techniques available, including spot welds for microscopic connections, seam welding for continuous joints, and advanced hybrid welders that blend laser energy with traditional welding methods for tough materials. These approaches work efficiently on a wide range of metals—think stainless steel, titanium, aluminum, and exotic alloys . The result is less downtime, consistent results, and the ability to weld even highly reflective or difficult materials that might challenge other welding machines .
How Laser Welding Machines Work
- • The basics of fiber laser and laser welding techniques
- • Spot weld, seam welding, and hybrid laser welders
- • Suitable materials: Stainless steel, titanium, aluminum, and more
The magic of a laser welding machine is in its precision. A fiber laser produces a narrow, concentrated laser beam that can be directed with pinpoint accuracy. Control systems adjust beam parameters for each application, whether you're making quick spot welds on battery connectors or seamless welds on automotive frames. Hybrid systems might combine laser energy with arc welding for extra penetration or to manage challenging alloy combinations.
This process generates a strong weld with little-to-no overheating, preserving the mechanical properties of the weld materials. It's especially beneficial for thin metals or temperature-sensitive assemblies in electronics and aerospace. Modern pulsed lasers even allow the welding of highly reflective materials such as copper or gold, further extending the practical use cases.
“Laser welding creates strong, precise joints with minimal heat input, reducing distortion and improving product quality.” — Welding Industry Expert
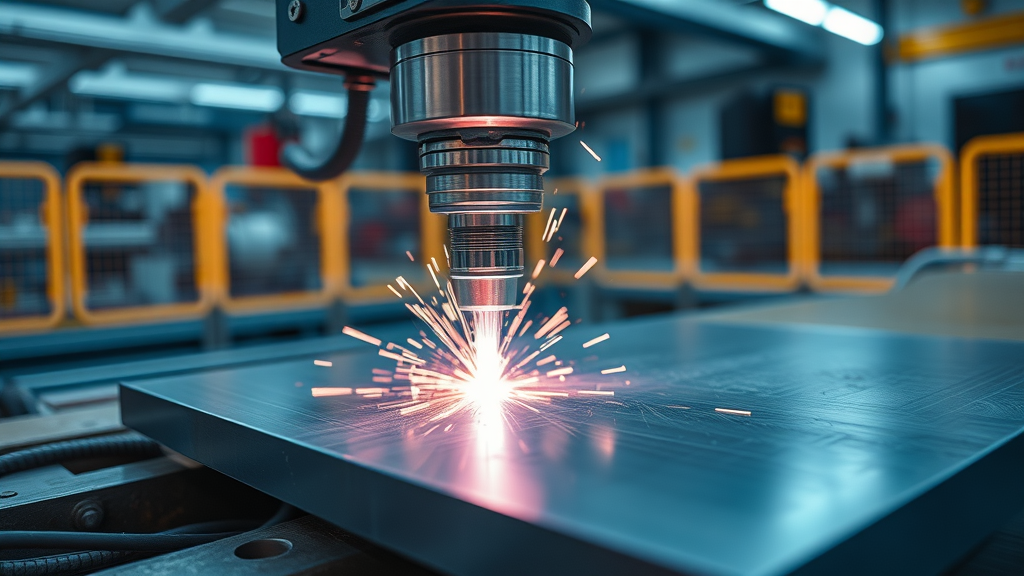
Laser Welding vs. Traditional Welding Machines: A Side-by-Side Comparison
Comparing laser welding systems with traditional welding machines (like MIG or TIG welders ) reveals why so many industries are investing in laser solutions. Laser welders offer unmatched placement accuracy and can automate a wide range of welding processes with less manual oversight.
Traditional systems generate more heat, which can cause warping, spatter, or internal stress in sensitive weld materials. Laser welds, by contrast, involve less heat input, resulting in superior weld quality and a cleaner working environment. With lower maintenance requirements, faster production cycles, and improved safety (less exposure to fumes), laser welding unlocks clear operational advantages.
Feature | Industrial Laser Welding | MIG/TIG Welding |
---|---|---|
Precision | High | Moderate |
Speed | Fast | Moderate |
Automation | Easily Automated | Limited |
Material Range | Broad | Moderate |
Heat Impact | Low | High |
Top Features of Industrial Laser Welding Machines
The advanced features of industrial laser welding machines empower manufacturers to push boundaries in both speed and productivity. Let’s look at the technological breakthroughs driving this transformation.
Fiber Laser Technology and Its Advantages
- • High beam quality
- • Lower power consumption
- • Maintenance efficiency
Fiber lasers are prized for their high beam quality , delivering tight, consistent energy that produces superior welds—whether it’s a fine spot weld on electronics or extensive seams on medical implants. These systems also offer lower power consumption and are more efficient to run than older types of lasers , translating to energy savings and reduced operational costs.
Maintenance is another standout advantage. The robust construction of fiber laser welders means less downtime and longer service intervals, allowing factories to sustain volume production and meet stringent deadlines. Their ability to weld a wide range of materials, including highly reflective metals, positions them at the leading edge of industrial fabrication worldwide.
Smart Welding System Integration
- • Real-time monitoring
- • Automated adjustment for consistent welds
- • Integration with laser cleaning solutions
Today's laser welding machines often include smart controls and advanced data monitoring. Real-time sensors track weld quality, detect anomalies, and automatically adjust laser parameters, ensuring every weld meets tight tolerances without the need for constant manual intervention. Such integration brings a new level of repeatability and quality assurance that traditional systems can’t match.
Smart systems also link with laser cleaning stations, making it easy to prepare and treat surfaces prior to welding. With seamless integration , operators can switch between cleaning and welding processes within the same work cell, boosting flexibility for a variety of manufacturing needs.
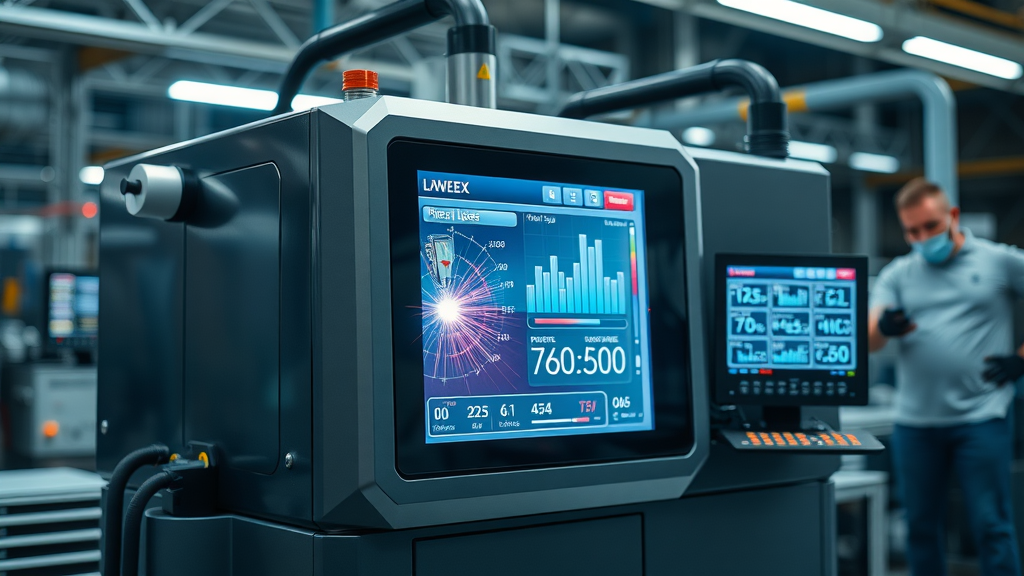
How to Choose the Right Laser Welder for Your Application
- • Assessing material compatibility (stainless steel, aluminum, specialized alloys)
- • Production scale and throughput needs
- • Required welding technique (spot weld, seam, hybrid)
- • Evaluating the wide range of welding solutions and systems
Selecting an industrial laser welder starts with understanding your material and production requirements. Do you need a system for joining stainless steel or more challenging alloys? Will your welder handle spot welds for electronics, full-length seams for automotive, or hybrid applications for aerospace components?
Consider your throughput and the variety of parts you plan to manufacture. High-volume production lines may benefit from fully automated, integrated welding solutions, whereas job shops might prefer flexible systems capable of welding a wide range of materials and geometries. Don’t overlook factory support, training, and the reputation of your chosen supplier—the right partner helps maximize your investment through ongoing service and education.
Industrial Applications and Use Cases for Laser Welding
The impact of industrial laser welding can be seen across numerous industries, where its precision and versatility outshine traditional welding machines . Laser welding systems are as essential to high-speed automotive production as they are to delicate electronics assembly or the stringent needs of medical device manufacturing.
Welding Process Innovation Across Industries
- • Automotive: Battery modules, chassis assemblies
- • Aerospace: Structural components, titanium parts
- • Electronics: Miniaturized assemblies
- • Medical: Surgical instruments, implants
In automotive factories, fiber laser welders join chassis and battery enclosures with unmatched speed and accuracy, helping manufacturers transition to EV platforms with less downtime. Aerospace production relies on laser welding's consistency for complex titanium and lightweight alloys on aircraft panels. Electronics firms benefit from the micro-precision of laser welders for assembling intricate sensors and circuit pathways.
In medical technology, the cleanliness and control of laser welds are vital for assembling sophisticated surgical tools and implants, ensuring patient safety and regulatory compliance. These examples illustrate why a wide range of industries are adopting advanced laser welding for both productivity and quality gains.
Range of Materials Supported by Laser Welding Systems
- • Stainless steel
- • Aluminum
- • Titanium
- • Exotic metals and composite materials
Laser welding systems support an impressive range of materials —from common metals like stainless steel and aluminum to specialty materials such as titanium and various exotic or composite alloys. This adaptability means one investment in a high-quality laser welding machine can meet the demands of multiple manufacturing sectors.
Even highly reflective materials that frequently cause issues with arc or resistance welders—like copper or gold—can be processed efficiently using pulsed or high-power fiber lasers. This expands the market potential for manufacturers, enabling agile production shifts and rapid innovation.
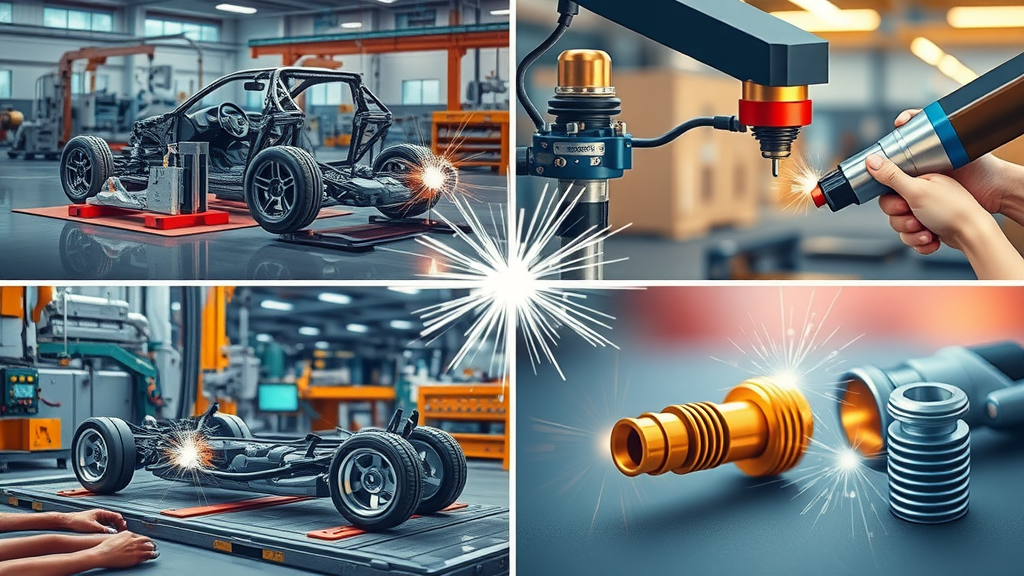
Pricing Overview: What to Expect with Laser Welding Machines
- • Key price drivers (wattage, automation, material range)
- • Investment vs. return analysis for manufacturers
- • Real-world savings: Lower energy, material, and rework costs
The cost of a laser welding machine is influenced by several factors—chief among them, laser power (wattage) , automaton level, and compatibility with various materials. Entry-level systems for prototyping or small parts might cost less, while full production cells with smart automation and real-time data analytics command a premium.
However, the return on investment (ROI) is often compelling. Many users find that the efficiency gains—lower scrap rates, faster cycle times, and reduced labor costs—generate paybacks within a year.
“The investment in a high-quality laser welding machine often pays for itself in less than a year through reduced labor and increased quality.” — Manufacturing CFO
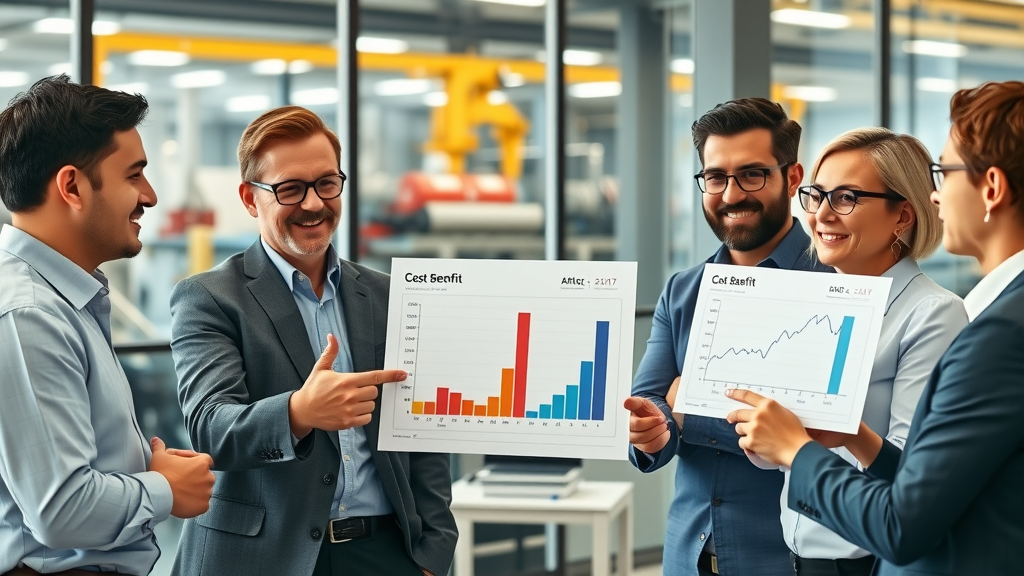
Customer Reviews: Experience with Industrial Laser Welders
- • User success stories from advanced manufacturing
- • Before/after metrics: Speed, accuracy, defect reduction
- • Client testimonials for fiber laser and laser welding solutions
Customers rave about the difference modern laser welders make in both quality and productivity. One automotive manufacturer cited a nearly 40% drop in production time after integrating a state-of-the-art fiber laser welding machine . In the electronics sector, clients have praised the dramatic reduction in assembly defects and the ability to miniaturize welds for next-generation smart devices.
Many businesses share stories of scaling up without expanding floor space, leveraging the automation of laser welding machines to improve throughput. Consistent, repeatable welds mean less waste and fewer product returns, while onboard analytics help identify and resolve bottlenecks. The consensus is clear: investing in laser welding systems delivers measurable improvements that traditional techniques simply can’t match.
People Also Ask About Industrial Laser Welding
Is laser welding stronger than MIG welding?
- Laser welding often produces stronger, more precise joints than MIG welding due to its concentrated energy and minimal heat-affected zone, especially in high-precision industrial settings.
Does a laser welder really work?
- Yes, laser welders are proven to produce reliable, repeatable welds across a wide range of metals and thicknesses, including difficult-to-weld materials.
How much does laser welding make?
- Laser welding machine operator salaries and business profitability can vary, but shops often report higher revenues and ROI due to premium service rates and increased productivity.
How thick steel can a laser welder weld?
- Modern industrial laser welding machines can weld steel sheets up to 25mm thick, depending on the laser power and welding system.
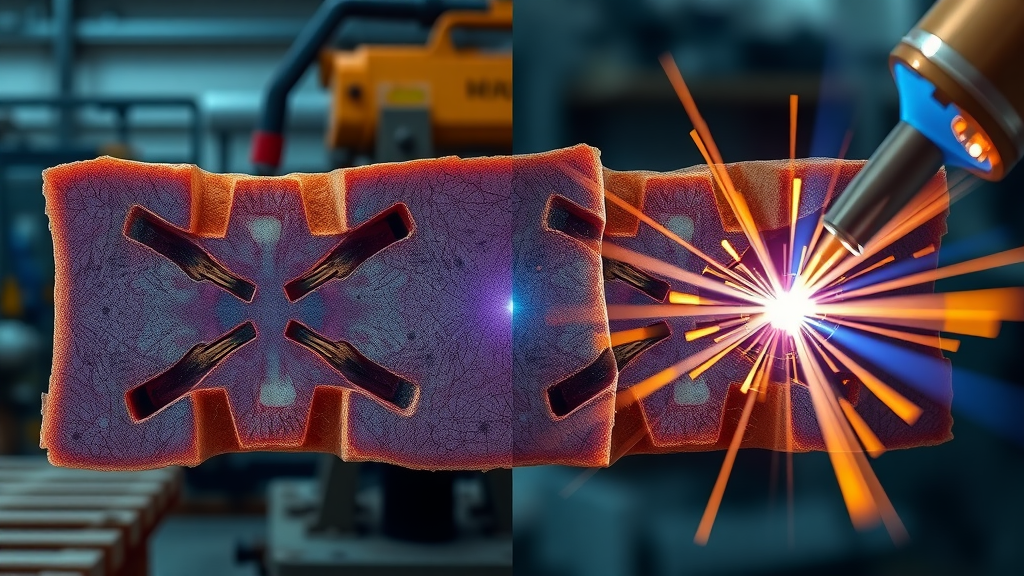
Unlocking Competitive Advantages with Advanced Laser Welding Solutions
- • Streamlining supply chains and improving lead times
- • Quality consistency for mission-critical projects
- • Wide range of customizable welding techniques and services
Adopting advanced laser welding solutions allows manufacturers to streamline supply chains, minimize lead times, and meet ever-tightening production specs. These systems enable a wide range of welding services—customized per part, project, or market—with built-in flexibility for future needs.
Most importantly, quality consistency becomes the norm rather than the exception. Whether you’re building safety-critical aerospace components or precision electronics, maintaining top-tier standards is vital for compliance and brand reputation. Laser welding provides the control and analytics to make that level of reliability attainable.
Industry Expert Advice: Best Practices for Implementing Laser Welding Systems
- • Assess production requirements and material handling
- • Invest in operator training and safety
- • Leverage data analytics for process improvement
Success with industrial laser welding hinges on clearly defining your production needs and ensuring a seamless match with chosen equipment. Always assess material flow, part handling, and overall line integration ahead of any investment. Train staff in both operation and laser safety, empowering them to maximize your system’s capabilities.
To continually improve weld quality and efficiency, leverage the data analytics provided by modern laser welders—these insights help optimize parameters and detect anomalies before they become issues.
“Commitment to continuous improvement ensures you stay ahead in an ultra-competitive market.”
Essential FAQs About Industrial Laser Welding
- • What safety precautions are necessary for laser welding?
- • How do fiber lasers compare to CO2 for welding performance?
- • What maintenance does a laser welding machine require?
- • Can an industrial laser welder handle both thick and thin materials?
Safety is paramount: always use protective eyewear and follow operational protocols. Fiber lasers generally outperform CO2 lasers with higher beam quality and lower running costs. Maintenance for laser welding machines mainly involves cleaning optics, checking cooling systems, and periodic calibration. With the right settings, one industrial laser welder can tackle a broad spectrum of material thicknesses and types.
- Watch real-world demonstrations of fiber laser welding machines performing high-speed, precision welds on stainless steel and aluminum.
This video offers a close look at the laser welding process in a clean industrial setting, complete with real-time footage of the weld formation and expert explanations. You'll see the precision and reliability that set laser welders apart from conventional alternatives.
Choosing the Right Industrial Laser Welding Partner
- • Importance of local, onshore support
- • Range of laser machining and welding services offered
- • Key considerations for reshoring manufacturing operations
Your journey to implementing industrial laser welding is only as smooth as the partner you choose. Local, onshore support ensures prompt service, ongoing training, and a welding service offering tailored to your project. Be sure to evaluate the supplier's expertise in both laser machining and welding, as well as their resources for quick turnaround and spare parts.
With today’s global supply uncertainties, many organizations are reshoring manufacturing. An experienced local provider can make this transition seamless, providing technology and service to support your evolving operations.
Ready to Transform Your Business with Industrial Laser Welding?
- Facing Tariff Pressures? It’s Time to Reshore Smarter. At Electronic Service Products, we specialize in precision laser machining solutions that meet the highest quality standards—onshore, on time, and on budget. Whether you're looking to reshore your manufacturing or avoid the mounting cost of overseas tariffs, we offer the speed, precision, and flexibility your supply chain demands. 👉 Call today 203-265-4167 or go to espcnc.com/request-a-quote
Now is the moment to modernize your operations—invest in industrial laser welding to cut costs, boost productivity, and reach new standards of quality. Contact our expert team to unlock your competitive edge.
Industrial laser welding is transforming manufacturing by offering unparalleled precision, speed, and efficiency. For a comprehensive understanding of this technology, consider exploring the following resources:
This resource provides an in-depth overview of laser welding processes, highlighting its advantages such as high precision, repeatability, and minimal maintenance requirements.
This article delves into the core principles of laser welding, discussing various types of lasers used and their specific applications in industrial settings.
If you’re serious about enhancing your manufacturing processes, these resources will provide valuable insights into the benefits and applications of industrial laser welding.
Write A Comment