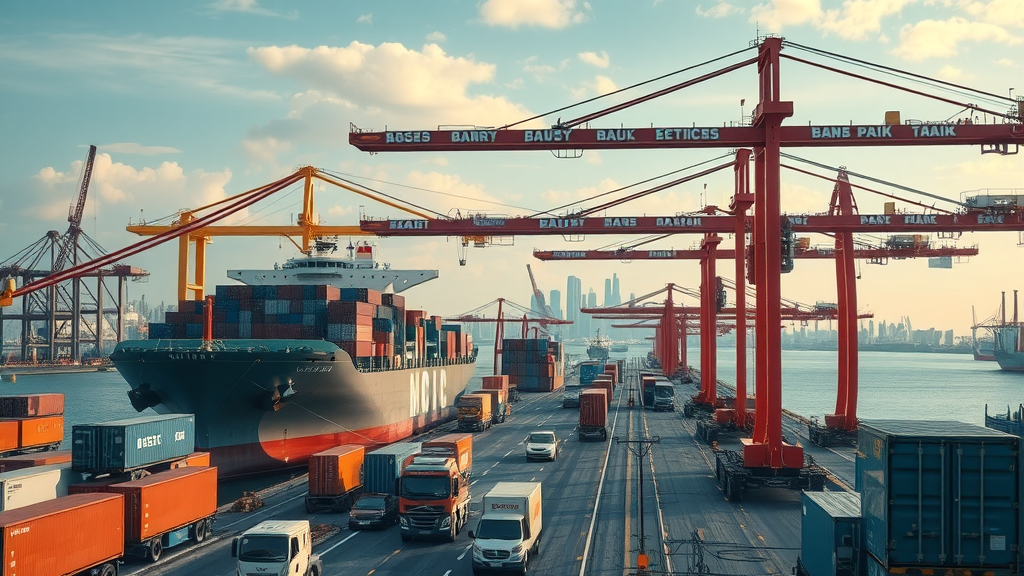
Did you know global supply chains absorbed an estimated $1.3 trillion in extra costs due to tariffs just between 2018 and 2022? Behind every product that travels from one country to another lies a complex web of tariffs and supply chain costs—factors now weighing heavier than ever on businesses and consumers. As international trade policies shift and trade wars intensify, the pressures on global supply chain operations and prices are fundamentally reshaping how business gets done. This article unpacks the true impact of tariff rate hikes , investigates how costs ripple across economies, and offers a look into emerging strategies that firms are adopting just to survive. Read on as we illuminate the interconnected burdens—often hidden from view—that shape the future of global trade and every good on a store shelf.
Unveiling the Hidden Costs: The True Impact of Tariffs and Supply Chain Costs
"According to the World Trade Organization, global supply chains faced an estimated $1.3 trillion in additional costs due to tariffs between 2018 and 2022—a burden passed down to companies and consumers alike."
Tariffs and supply chain costs often operate behind the scenes, but their influence is felt in every corner of the modern marketplace. Whether you’re a manufacturer procuring raw materials or a consumer purchasing everyday goods, the ripple effects of tariffs on imported goods are hard to ignore. When governments institute high tariffs, the most immediate reaction is a spike in the cost of goods imported , impacting everything from electronics to clothing. Companies must either absorb these increased expenses or pass them down the supply chain, culminating in higher prices for the end user.
The challenge doesn’t stop there— supply chain operations are forced to reevaluate logistics, supplier partnerships, and production timelines to mitigate these extra burdens. Free trade agreements once granted smooth movement of goods; now, with escalating trade wars and retaliatory policies, businesses are forced to operate in a lopsided and unpredictable global market. Ultimately, these pressures have a compound effect, reshaping business models and causing supply chain managers to adopt new cost-mitigation strategies just to stay competitive.
Understanding Tariffs and Supply Chain Costs in Global Trade
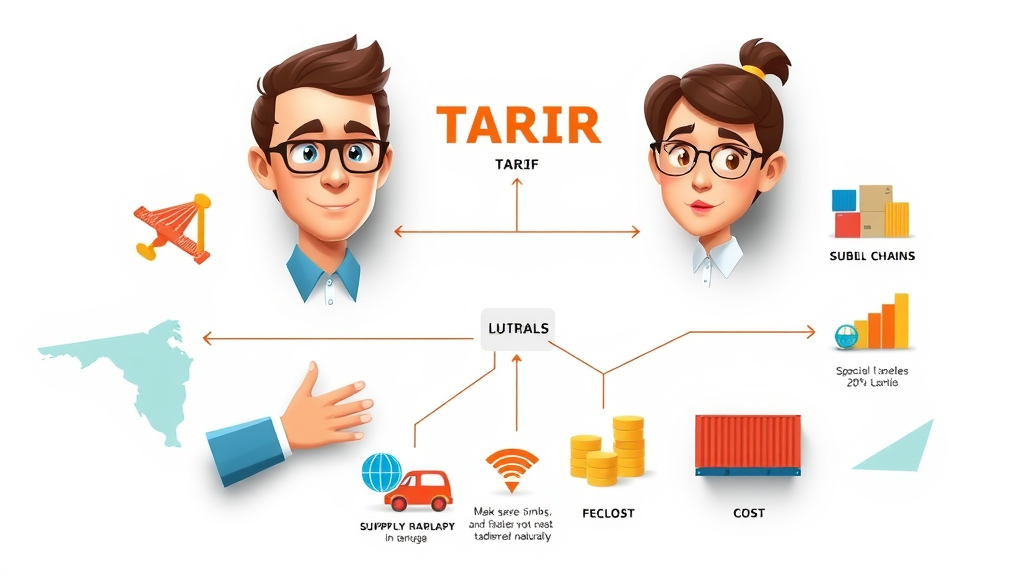
- Defining tariffs and supply chain costs: Tariffs are government-imposed taxes on goods as they cross country borders, while supply chain costs encompass all expenses from procurement to delivery—procurement, manufacturing, shipping, customs, and logistics.
- Exploring their interdependence: When tariffs rise, so do supply chain costs. The relationship is cyclical; higher import tariffs lead to increased expenses in every stage of the supply chain management process, creating challenges for companies reliant on global sourcing.
- How tariffs reshape supply chain operations: Tariff rate changes force businesses to rethink sourcing strategies, renegotiate with suppliers, shift production locations, and navigate new regulatory landscapes. The dynamic interplay between trade policy and supply chain decisions has become a key determinant in global competitiveness.
As markets adapt to higher tariffs, companies may shift from foreign suppliers to more local sources, a move that can disrupt established partnerships. The introduction of new tariffs can also cause trade patterns to shift abruptly, challenging established operational flows and causing logistical headaches. This ever-changing environment underlines how closely tariffs and supply chain costs are intertwined, requiring businesses to remain agile and informed.
The Evolution of Global Supply Chain Operations: Tariffs as a Game Changer
Shifting Dynamics in Global Supply Chains
- Increased costs for component sourcing: Tariff increases on key raw materials like steel, microchips, and textiles prompt a surge in component and finished good prices across multiple industries.
- Shift in supplier relationships: Businesses are forced to reevaluate suppliers, seeking alternatives outside high-tariff nations, which strains long-standing partnerships and destabilizes procurement cycles.
- Ripple effects on global supply and local economies: The impact of tariff shock isn’t limited to multinationals—it spreads to local economies, vendors, and logistics providers, influencing decisions on job creation, pricing, and sourcing for years to come.
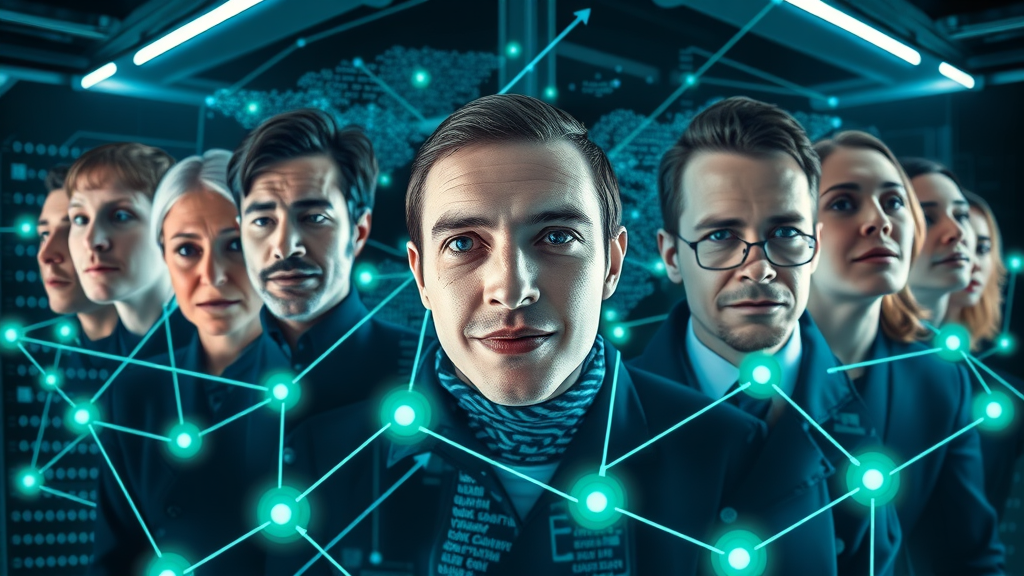
The international supply chains of today look vastly different from a decade ago. Companies are forced to track shifting tariff policies across all countries where they do business. The search for stability leads some organizations to near-shoring (moving production closer to the point of consumption) or even reshoring (bringing production back home), upending the traditional model of relying on far-flung suppliers for cost savings. Small and mid-sized firms, especially those in North America, may struggle the most with sudden cost increases as they lack the negotiating power to absorb or pass along higher expenses.
This constantly evolving scenario means even resilient supply chain models must adapt to new risks in real-time. The once-stable foundation provided by free trade agreements is now undermined by uncertainty stemming from retaliatory policies, changing tariff rates, and global disputes. Businesses who fail to adapt could face disrupted operations, rising costs, or, ultimately, a loss of global competitiveness.
High Tariffs and the Trade War: Recent Developments
- United States vs. China—trade war origins and impact: The escalation began with the U.S. imposing tariffs on hundreds of billions of dollars’ worth of Chinese imports, prompting reciprocal action from China. This disrupted the sourcing of electronics, machinery, and everyday consumer goods worldwide.
- Key sectors: Industries such as steel and aluminum , electronics, and finished consumer goods have seen some of the most pronounced effects, with drastic increases in the cost of raw materials and finished products alike.
- Examples from Canada and Mexico: Neighboring nations responded with their own tariffs, affecting goods like automobiles, agricultural products, and steel, further complicating supply arrangements and ratcheting up costs throughout North America.
The recent trade war between the United States and China marked a new era of uncertainty in global trade . Industries that enjoyed stable, predictable sourcing due to free trade are now navigating a patchwork of new tariffs and counter-tariffs. Major exporters have responded by seeking new partners, while industries like automotive and technology feel the sting of rising costs for both imported components and finished goods. These rapid changes amplify the pressure on global supply chains to innovate or risk being left behind.
For North America, the result of tit-for-tat tariff policies has meant volatile prices, unpredictable lead times, and new hurdles for companies that once relied on seamless, cross-border trade. The experience of Canada and Mexico highlights the complicated consequences of protectionist policies, with businesses forced to find creative solutions for sourcing, logistics, and risk management.
Tariffs and Supply Chain Costs: The Domino Effect on Supply Chain Operations
Sector | Pre-Trade War Tariff Rate | Post-Trade War Tariff Rate | Estimated Supply Chain Cost Increase (%) |
---|---|---|---|
Steel and Aluminum | 2-4% | 15-25% | 20-35% |
Consumer Electronics | 5-7% | 15-20% | 10-25% |
Automotive Components | 2.5% | 10-15% | 5-18% |
Agricultural Products | 0-5% | 10-22% | 5-15% |
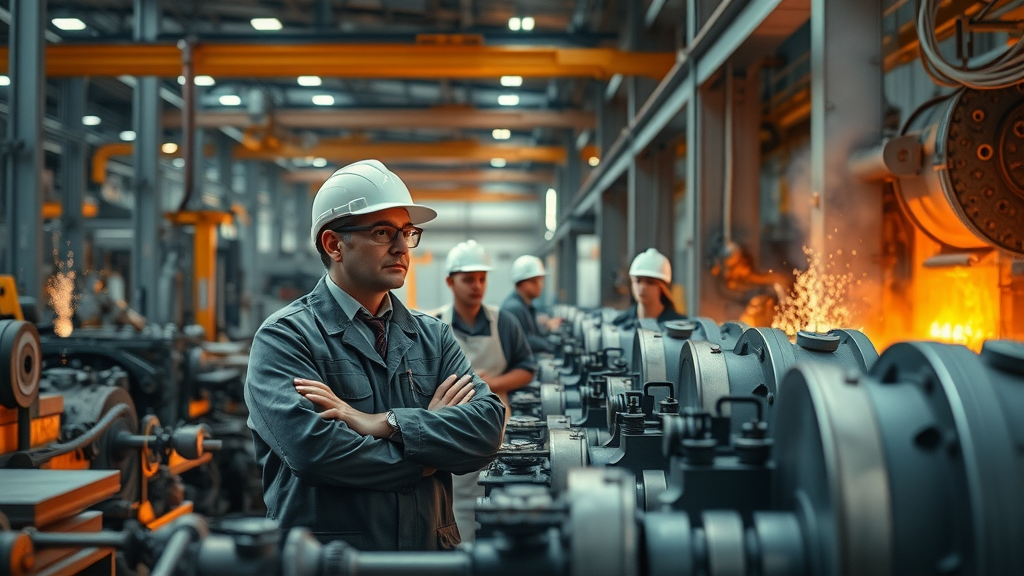
Case Study: Steel and Aluminum in Global Supply Chains
- Tariff implementation on metals: New import tariffs on steel and aluminum drastically increased the cost of these crucial raw materials, disrupting industries across construction, automotive, and manufacturing globally.
- Direct impact on manufacturing and construction: Higher material costs forced manufacturers to increase prices or find alternative suppliers, often at further expense and operational risk.
- Consequences for global supply chain efficiency: Extended lead times, production delays, and reconfigured logistics have collectively undercut efficiency and heightened uncertainty for those reliant on internationally sourced metals.
"When tariffs increased on imported steel, our raw material costs rose over 20%, impacting every segment of our supply chain operations." — Supply Chain Director, Major US Manufacturer
This case study of steel and aluminum illustrates how even a single policy change can send shockwaves throughout a heavily interconnected supply chain. Companies were forced to reconsider the balance between sourcing domestically and relying on cheaper imports, juggling cost increases against the risk of further tariff shock . Construction projects saw thin margins evaporate, while manufacturers scrambled to diversify sourcing and renegotiate contracts. In each case, the compounding effect of tariffs on raw materials was magnified at every subsequent step in the value chain.
The lesson is clear: true supply chain resiliency now means planning for uncertainty, particularly when high tariffs or protectionist rhetoric threatens the flow of essential materials. Firms must weigh the reliability and price stability of local versus foreign suppliers, a calculus further complicated by evolving trade policies and the specter of ongoing trade tensions.
Reciprocal Tariffs and Supply Chains: Strategies and Realities
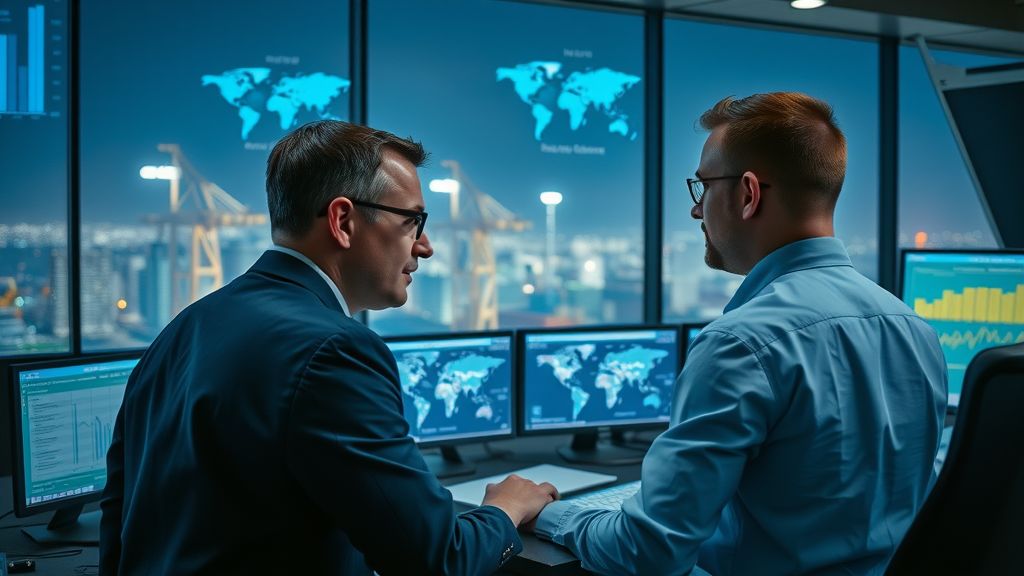
- Supplier diversification across supply chains: Reducing over-reliance on any one country or vendor mitigates risk from sudden tariff rate changes or trade disruptions.
- Near-shoring and re-shoring in global supply: Moving production and sourcing closer to final markets reduces exposure to international tariff shock and streamlines logistics.
- Digitalization and risk management in supply chain operations: Technologies like AI, real-time data analytics, and blockchain enable businesses to anticipate risks, assess total landed costs, and optimize supply chain management decisions in an ever-changing global trade environment.
Facing the reality of reciprocal tariffs—a policy move where countries respond to each other's measures with similar action—companies are adopting new tools and strategies to minimize disruptions. Diversifying suppliers helps distribute risk, ensuring that if one channel becomes prohibitively expensive or blocked, alternatives are already in place. For many businesses, near-shoring or re-shoring offers better control over supply chain operations, greater consistency, and resilience to sudden tariff rate or regulatory changes.
The embrace of digital technology in supply chain management has also become a defining factor for success. Sophisticated tools, from predictive analytics to full supply chain visibility platforms, empower teams to respond to issues before they escalate. By building redundancy and data-driven decision processes into chain operations , firms can better weather volatility, safeguard profit margins, and maintain competitive advantage in global markets punctuated by frequent trade policy shifts and reciprocal tariff threats.
Coping with Uncertainty: Best Practices for Mitigating Supply Chain Costs
- Strategic partnerships: Collaborative relationships with suppliers, customers, and logistics providers drive flexible solutions, boost reliability, and facilitate joint risk mitigation strategies.
- Advanced forecasting for global supply chains: Leveraging AI and big data enables more accurate projections of demand, potential tariff risks, and transportation costs, supporting proactive rather than reactive management.
- Technology adoption in chain operations: Integration of automation, IoT tracking, and digital procurement tools streamlines processes and builds resilience against sudden interruptions or cost spikes within global supply chain networks.
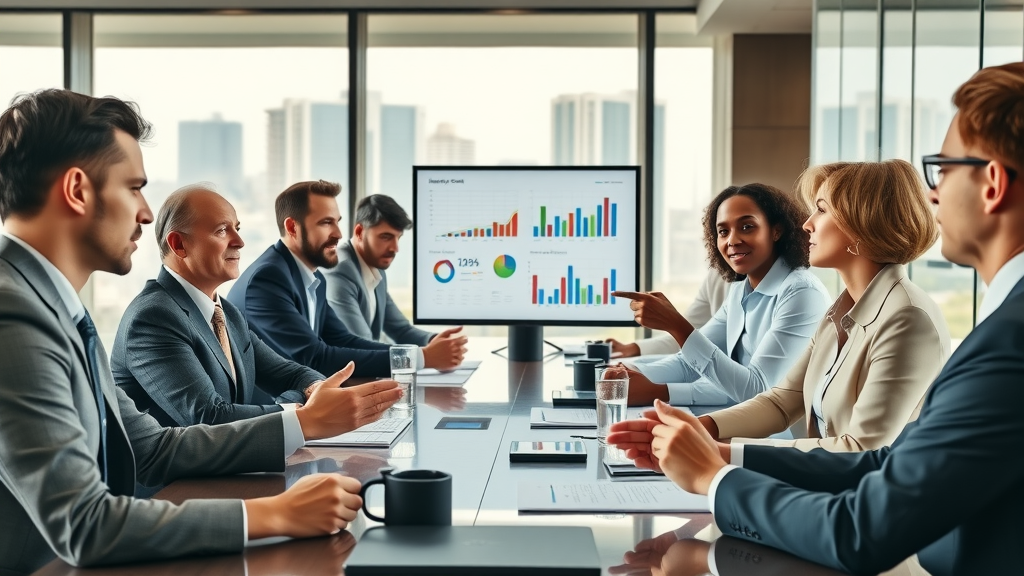
In periods of uncertainty, the best-performing companies set themselves apart by their investment in technology and relationships. Those who partner deeply with suppliers can negotiate better prices, find innovative solutions to shared problems, and build systems for information sharing that provide mutual benefit. The predictive power of advanced analytics, meanwhile, allows organizations to identify emerging risks and opportunities long before they show up on the balance sheet.
People Also Ask
How do tariffs affect the supply chain?
Tariffs directly raise the cost of importing goods and raw materials, which increases production and supply costs for companies in the global supply chain . This often leads businesses to find alternative sourcing, renegotiate contracts, or pass additional costs on to consumers. Long-term, higher tariffs can change the structure and flow of entire supply chains, sometimes leading to less efficiency and increased operational complexity.
By elevating costs on critical components, tariffs can force manufacturers to reconsider the viability of certain supplier relationships. This ripple effect may change the landscape of global sourcing and even prompt companies to shift production locations in search of more favorable trade environments. The result: a less predictable, often more expensive operating context for businesses around the world.
Do tariffs affect shipping costs?
Yes, tariffs can indirectly increase shipping costs . When tariffs drive up the price of goods or raw materials, companies often seek out new suppliers in different countries or regions to minimize expenses. This change in trade patterns can result in unexpected shipping routes, more complex logistics, and varied compliance requirements—all of which combine to raise overall transportation costs. These higher costs can be further exacerbated by longer delivery times and increased customs fees.
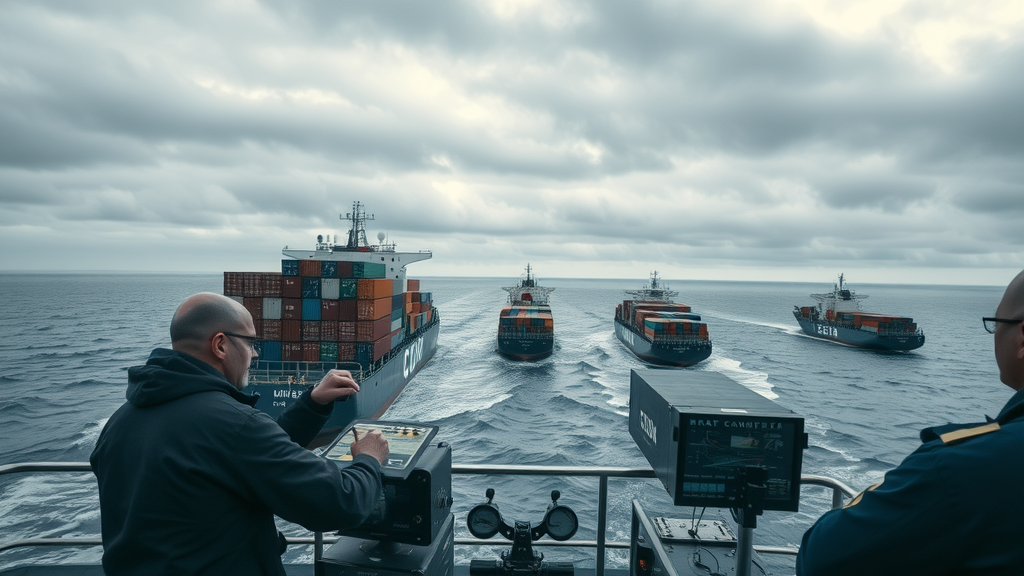
What does a tariff do to supply and demand?
A tariff acts as an additional cost on imported goods, reducing their supply and making them more expensive compared to domestic products. As a result, demand for imported goods typically decreases, while demand for potentially less costly domestic alternatives rises. This shift in supply and demand dynamics can lead to price increases, reduced consumer choice, and changes in market competitiveness, especially for companies operating within tight supply chains.
What are supply chain costs?
Supply chain costs include all expenses associated with moving a product from the source to the end customer. Key elements include sourcing, manufacturing, warehousing, transportation, customs duties (like tariffs), and last-mile delivery. Effective supply chain management aims to minimize these costs without sacrificing quality, speed, or reliability, but rising tariffs and global uncertainties can make this balancing act significantly more challenging.
Tariffs and Supply Chain Costs: The Future of Global Supply Chains
- Emerging trends in global supply chains: Businesses are accelerating investments in digital transformation, resilience planning, and sustainability initiatives to safeguard against recurrent tariff shocks and volatile trade policies.
- Sustainability vs. cost reduction: With higher tariffs inflating costs, companies face the dual challenge of seeking cost savings while pursuing greener supply chain strategies and meeting new regulatory standards.
- Long-term effects of persistent high tariffs: Continued tariff escalation could lead to diminished global trade flows, more localized production, and increased vulnerability to supply disruptions, fundamentally altering how the world's supply chains operate.
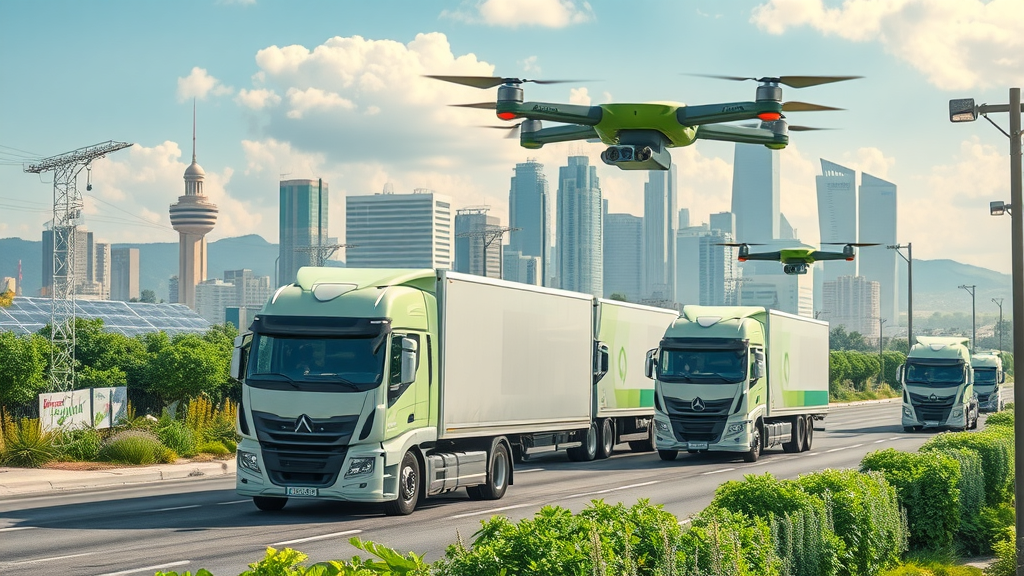
The future of global supply chains will hinge on how effectively organizations can adapt to policy-driven cost changes while innovating along the way. From greener logistics operations to real-time digital monitoring, growing investments in technology and new business models are already redefining what’s possible under a new regime of persistent tariff risk and global uncertainty.
Sustainability will increasingly factor into decisions traditionally dominated by cost concerns. Companies must balance financial goals with consumer expectations and environmental mandates, creating a transformative backdrop where agility and forethought are key to enduring and thriving in tomorrow’s market landscape.
FAQs on Tariffs and Supply Chain Costs
-
Q: What industries are most affected by tariffs and supply chain costs?
A: Industries relying heavily on imported raw materials or components—such as automotive, electronics, consumer goods, and agriculture—are especially vulnerable to tariff-driven cost increases. Sectors like construction and manufacturing, which depend on steel, aluminum, and globally sourced parts, are often among the hardest hit. -
Q: Can technology offset the impact of tariffs on global supply chains?
A: Yes, digital technologies like supply chain visibility platforms, AI-driven forecasting, and blockchain can help companies monitor risks, optimize logistics, and identify cost-saving opportunities, all of which help offset tariff impacts. -
Q: Are reciprocal tariffs sustainable in global trade?
A: Sustained reciprocal tariffs create volatility and complexity, challenging the efficiency of global supply chains . While they can protect specific domestic industries in the short-term, they tend to disrupt trade flows and reduce overall global economic growth.
Key Points in Managing Tariffs and Supply Chain Costs
- Prioritize flexibility in supply chain operations: Stay agile by maintaining diverse sourcing and adaptable logistics frameworks to quickly respond to shifts in tariff rates and global policies.
- Invest in digital supply chain tools: Embrace technology that enables real-time risk assessment, demand forecasting, and cost management for greater control.
- Foster strong, diverse global supply relationships: Proactively seek partnerships across multiple geographies, reducing over-reliance on any single country or vendor in an unstable international trade environment.
Share Your Perspective on Tariffs and Supply Chain Costs
"Every business, regardless of scale, is now affected by tariffs and supply chain costs. It's time for industry voices to steer the policy debate."
- Have insights to share on global trade? Let's talk—call us at 203-271-7991 to explore contributing an article.
Don’t let tariffs derail your operations—embrace technology, foster flexibility, and stay engaged in the evolving global trade debate for supply chain success.
Tariffs and supply chain costs are increasingly impacting global trade, prompting businesses to seek effective strategies to mitigate these challenges. The article “Tariff Impact on Supply Chain: Costs, Risks & Strategy” by Jabil offers a comprehensive analysis of how tariffs affect supply chain networks and provides actionable strategies for businesses to adapt. Additionally, “US Tariffs: Impact on Supply Chains and Procurement Strategies” by Tradogram delves into the specific effects of U.S. tariffs on procurement processes and outlines methods to manage associated risks. For a broader perspective, “How Tariffs Are Reshaping Global Supply Chains in 2025” by SupplyChainBrain examines the evolving landscape of global supply chains in response to tariff implementations. If you’re serious about understanding and navigating the complexities of tariffs and supply chain costs, these resources will provide valuable insights and strategies.
Write A Comment