Did you know? Over 70% of manufacturers cite precision and repeatability as their top reason for switching to laser welding solutions. In today’s fierce global market, the difference between success and falling behind often comes down to advanced technology. If you're struggling with outdated welding systems, costly defects, or long overseas lead times, laser welding solutions might be the game-changer you need. This article reveals exactly how modern laser welding is transforming manufacturing across industries—and shows you the fix you’ve been searching for.
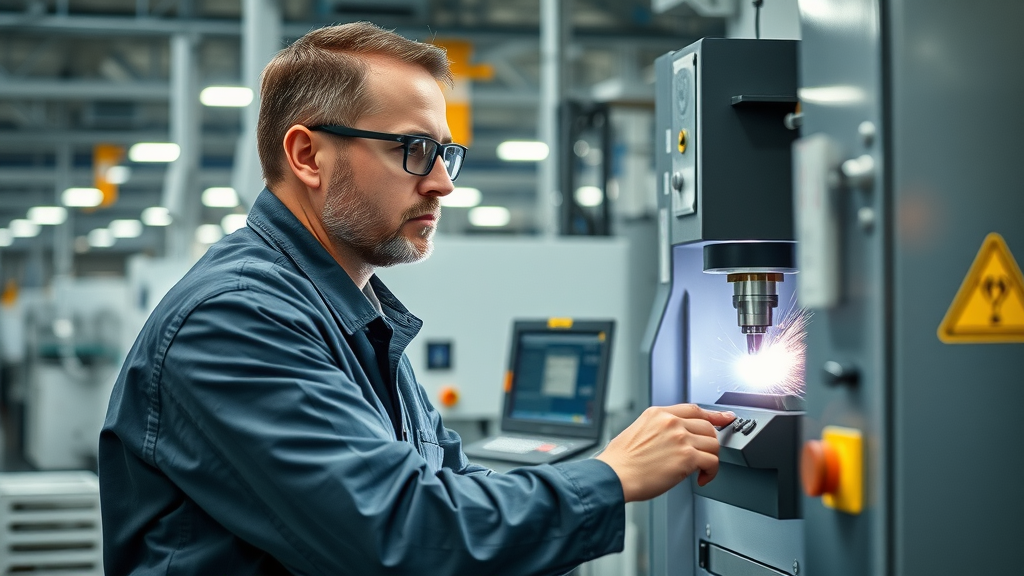
Laser Welding Solutions Transform Modern Manufacturing—Why You Can't Afford to Overlook Them
- Did you know? Over 70% of manufacturers cite precision and repeatability as their top reason for switching to laser welding solutions. In a global industry where quality and quick turnaround are paramount, outdated welding systems can leave you falling behind.
Across the manufacturing world, precision, repeatability, and the ability to quickly adapt production lines are no longer luxuries—they’re business essentials. Laser welding solutions deliver a level of performance traditional welding processes simply can’t match. Manufacturers who adopt these systems consistently report significant reductions in defects, shorter cycle times , and greater design freedom.
If your production relies on reliable weld seams—whether for small, intricate medical devices or robust automotive components—laser welding outpaces mechanical joining, soldering, and older welding systems at every turn. Imagine achieving flawless welds with minimal heat input, enabling you to bond a wide range of materials with exceptional aesthetics and strength. Whether you need rapid prototyping or large-volume production, laser welding’s flexibility provides a strategic edge—and helps keep your manufacturing onshore, nimble, and competitive.
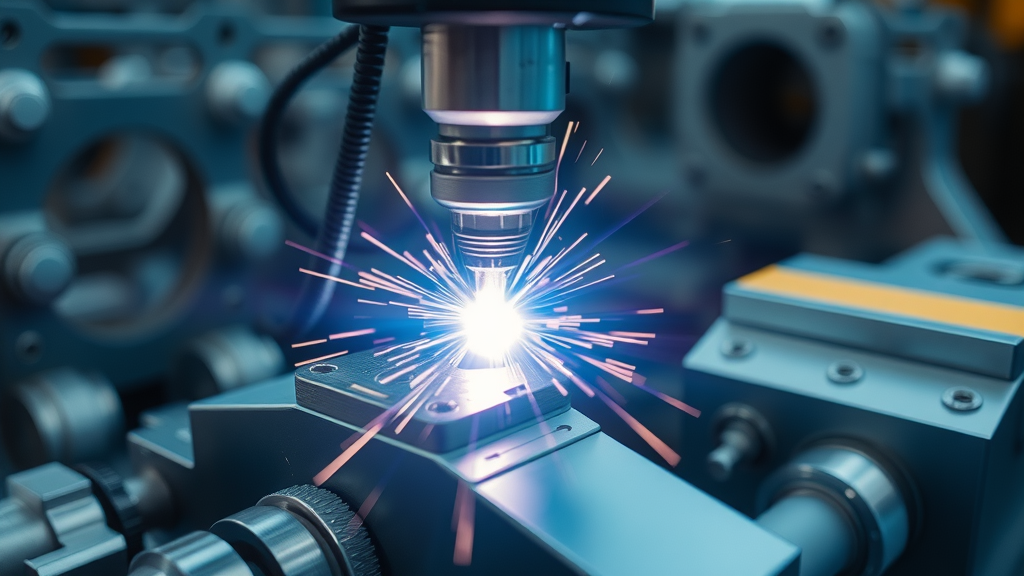
What You'll Learn About Laser Welding Solutions and How They Address Manufacturing Challenges
- How laser welding solutions outperform traditional methods
- Key features and benefits tailored for plastic welding, medical device manufacturing, and beyond
- Real-world examples showing the flexibility of laser plastic welding
- Which welding systems align best with your production goals
- How advanced welding solutions help you reshore, reduce costs, and boost precision
- Answers to the most common laser welding questions
This guide to laser welding solutions will demystify the technology, provide practical advice for choosing the right welding system, and reveal how to overcome global supply chain challenges. From plastic welding in medical devices to robust robotic welding for electronics and automotive—and everything in between—you’ll find expert insights tailored to your sector. Want to unlock better quality, streamlined workflow, and faster delivery? Read on for the competitive fix manufacturing teams everywhere are relying on.
Understanding Laser Welding Solutions: Technology, Process, and Key Advantages
How Laser Welding Works: The Science Behind Laser Beam Technology
- Laser beam precision and control
- Difference between laser welding and traditional welding solutions
- Energy efficiency and minimal heat impact
Laser welding solutions leverage focused beams of light—known as laser beams—to join materials with extraordinary control and minimal heat effect. The laser beam is directed through welding optics onto the materials, creating highly precise, clean, and repeatable weld seams . Unlike arc welding and other thermal methods, this process generates only a tiny heat affected zone , preserving the base material’s properties and supporting a wide range of applications from thin plastics to challenging metals.
In addition to their accuracy, laser welding systems boast shorter cycle times and lower maintenance compared to many traditional welding solutions. The advanced laser welding process reduces the need for extensive post-processing, resulting in outstanding exceptional aesthetics and less overall waste. Modern lasers are also highly energy efficient, making them a sustainable choice as well as a practical one.
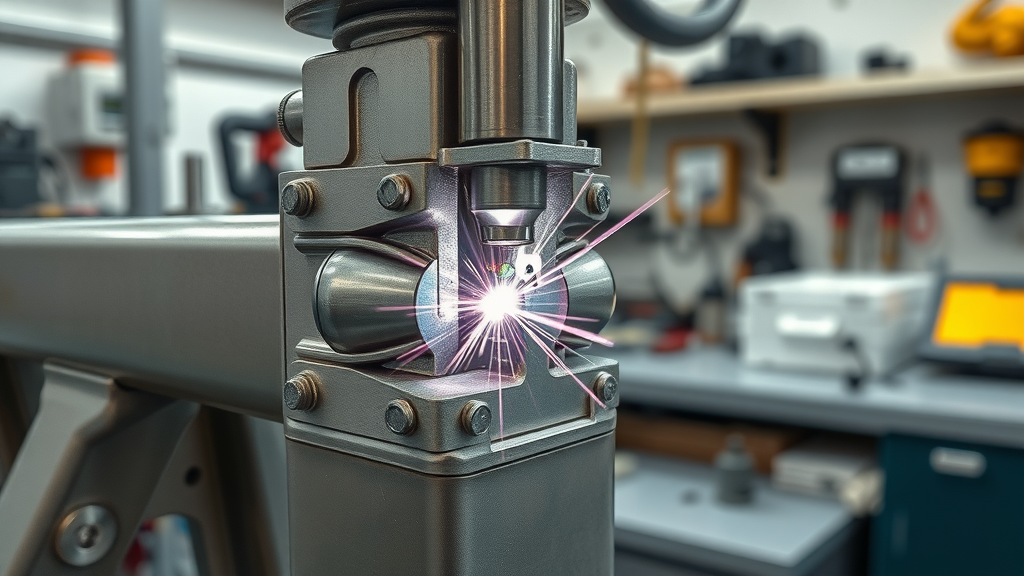
Types of Laser Welding Solutions—From Laser Plastic Welding to Metal Applications
- Laser plastic welding: definition and use cases
- Polymer welding and applications in medical devices
- Metal laser welding systems vs. robotic welding
Laser welding solutions are as versatile as they are precise. Laser plastic welding has become mission-critical for sectors such as automotive, electronics, and medical device manufacturing, where seamless, leak-proof bonds are non-negotiable. Polymer welding harnesses laser technology to join clear or opaque plastics—supporting innovation without sacrificing structural integrity or biocompatibility .
On the metals front, laser welding systems rival—and often outperform—robotic welding in speed, accuracy, and ability to accommodate difficult geometries. Whether you’re building a prototype or scaling to high-volume runs, the best solution often combines laser welding precision with automation or even robotic welding arms for maximum throughput and consistency.
"Laser welding solutions give us unmatched flexibility, allowing rapid prototyping and high-volume production without sacrificing quality." – Manufacturing Lead, Medical Device Industry
Key Features and Benefits of Modern Welding Systems
Precision, Speed, and Quality: Why Laser Welding is the Top Welding Solution
- Clean, consistent welds with minimal distortion
- Reduced finishing costs through pinpoint accuracy
- Wide range of materials supported, including plastics and metals
With laser welding solutions , manufacturers experience tight tolerances and virtually flawless weld seams . Laser welds are known for their precision, producing minimal spatter and distortion—a crucial factor when joining delicate medical devices or advanced electronics. The superior control delivered by modern welding optics ensures consistent welding results across every batch, reducing costly errors and rework.
Because laser-generated joints are so clean, post-process finishing is often unnecessary, trimming both costs and production time. The technology accommodates a wide range of materials—plastics, metals, or even hybrids—while supporting intricate 3D joins and advanced design freedom that other welding processes simply can’t handle on their own.
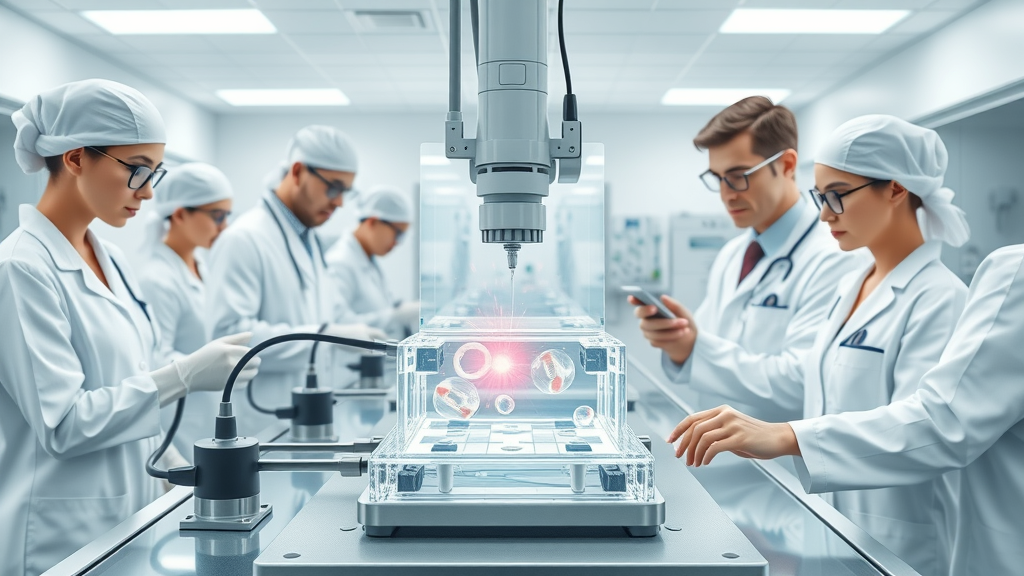
Laser Welding Solutions for Medical Devices and Regulated Industries
- Biocompatibility and contamination-free joining
- Automated documentation and traceability
- Compliance with industry standards
In medical device manufacturing, even the slightest contamination or misalignment can result in catastrophic product failures. Laser welding offers biocompatible, contamination-free joining , crucial for life-saving instruments. Documentation and traceability are streamlined as modern welding systems automatically record process data, helping you prove compliance with strict healthcare and regulatory standards.
Industry leaders like branson laser and Electronic Service Products provide advanced solutions for this high-stakes market. These systems are designed to handle everything from injection-molded polymer welding to miniature metal joins. Automated features, such as integrated inspection and robotic welding modules, add additional assurance, minimizing human error and guaranteeing reliability.
Criteria | Laser Welding Solutions | Conventional Welding |
---|---|---|
Precision | Extremely High | Medium |
Cycle Time | Short | Longer |
Heat Affected Zone | Minimal | Extensive |
Suitable Materials | Wide range | Limited |
Maintenance | Low | Medium-High |
How to Identify the Right Welding System: Questions to Guide Your Search
- What materials and product specs do your applications demand?
- Is laser welding compatible with your automation or robotic welding needs?
- Scale: Are you building prototypes or full production runs?
- Does your supply chain benefit from onshore, quick-turn laser welding solutions?
Choosing the ideal welding system begins with understanding your product’s material requirements and production scale. Ask if your workflow demands seamless plastic welding for automotive or leak-proof joints for sensitive medical device assemblies. Determine if you need a standalone machine or a system integrated with robotic welding arms for 24/7 high-volume capability.
Evaluate your current and future production volumes. Will rapid prototyping, small-batch runs, or fully-automated high-output lines serve you better? Finally, examine if bringing manufacturing onshore with reliable, responsive laser welding solutions can help reduce tariffs, cut lead times, and give you unmatched quality control. Consulting experts in welding systems such as Electronic Service Products ensures you make the smartest investment for your business.
Laser Plastic Welding: Industry Examples and Emerging Applications
Plastic Welding for Automotive, Medical, and Electronic Devices
- Leak-proof medical device seals
- Lightweight automotive components
- Sealed enclosures for sensitive electronics
Laser plastic welding has unleashed a new era of design freedom for industries that depend on strength and reliability in compact or complex forms. In medical device manufacturing, it enables the creation of leak-proof, sterile enclosures without using adhesives that could compromise safety. Automotive manufacturers leverage this technology for lightweight, precise parts that enhance fuel economy without sacrificing durability.
For electronics, laser welding solutions provide perfectly sealed compartments to safeguard sensitive circuits against moisture, dust, and vibration. The result: smarter, safer products that exceed consumer and regulatory expectations. From mobile gadgets to life-critical diagnostic tools— plastic welding is at the heart of innovation.
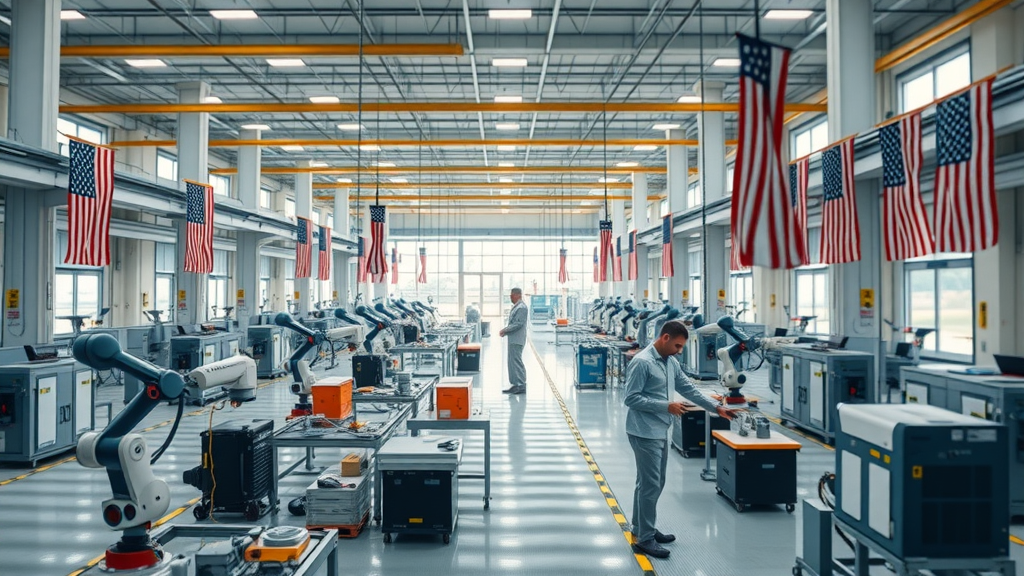
Choosing the Right Laser Plastic Welding Approach for Your Needs
- Transmission welding for clear/opaque plastics
- Contour welding for complex 3D joins
- Mask and quasi-simultaneous welding
Not all laser plastic welding approaches are created equal. Transmission welding is favored for joining clear and opaque thermoplastics—common in medical and automotive applications. It passes the laser beam through one material, heating the interface for a perfect join. Contour welding excels in complex 3D assemblies—like connectors and housings—where flexibility and precise pathing matter most.
For intricate or multi-point joints, techniques like mask welding and quasi-simultaneous welding deliver unparalleled consistency and speed. These methods combine broad area heating with pinpoint control, giving product designers maximum latitude without sacrificing weld quality. Leading welding solutions providers help match you with the process that best aligns with your goals, materials, and industry standards.
Overcoming Supply Chain Disruptions with Onshore Laser Welding Solutions
Reducing Tariff Risks and Lead Times with U.S.-Based Production
- Faster fulfillment and improved control of quality
- Flexibility for low- or high-volume runs
- Cost advantages over overseas manufacturing
Global disruptions and rising import tariffs have manufacturers looking stateside for greater control. Onshore laser welding solutions slash delivery timelines, minimize logistical risk, and tighten quality oversight. Quick-turn, small production or agile high-volume output can all be achieved when you work with a responsive U.S.-based partner.
Getting rid of long-distance, overseas dependencies means you’re not only protected from sudden regulatory shifts but also positioned to pivot fast—whether you need prototypes, product line updates, or full-scale production. With laser welding systems in modern American facilities, savings multiply through faster cycle times, lower transportation costs, and fewer product defects.
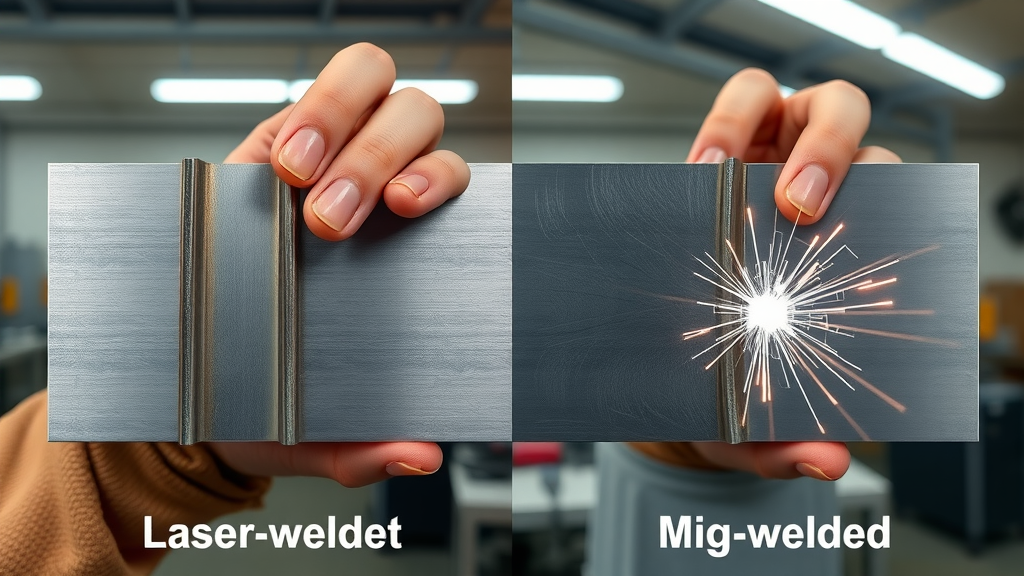
"Reshoring with onshore laser welding solutions has shaved weeks off our delivery timelines, slashed tariff exposure, and let us focus on zero-defect quality." – Operations Manager, Electronics Sector
People Also Ask: Your Top Laser Welding Solutions Questions Answered
How much does laser welding cost?
- Laser welding costs vary based on project scale, materials, and part complexity. Entry-level setups begin at a few thousand dollars, while advanced automated welding systems may reach six figures. For accurate pricing, request a custom quote tailored to your needs.
What are the downsides of laser welding?
- While laser welding offers high precision and speed, initial setup costs can be higher than traditional methods. It also requires skilled operators and regular system maintenance to perform optimally.
Is laser welding stronger than MIG welding?
- Laser welding can create stronger joints than MIG when correctly applied, especially in thin materials or dissimilar metal welding situations. It also offers greater precision and less heat-affected deformation.
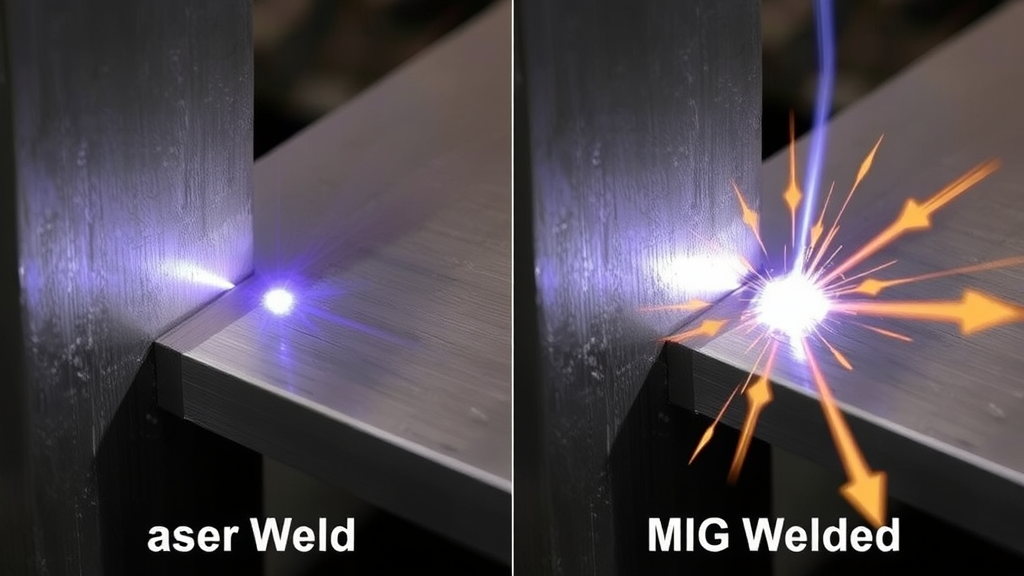
How thick of material can a laser welder weld?
- Laser welding solutions are typically ideal for materials up to 12mm thick. Some systems handle thicker materials, but the best results are seen in precision applications for thin to medium-gauge metals and plastics.
Frequently Asked Questions on Laser Welding Solutions
- Can laser welding solutions handle both plastics and metals?
- What kind of training is needed for operators?
- Are laser welding systems energy efficient compared to conventional welding?
- How do I maintain a laser welding system for maximum uptime?
- Is robotic welding integration straightforward?
Laser welding solutions are designed for both plastic welding and metal joining, making them highly versatile across industries. Operators benefit from user-friendly interfaces, but initial training is essential to master precision settings and system safety. In terms of efficiency, modern welding systems consume less energy compared to older approaches, supporting sustainable manufacturing goals. Regular cleaning and routine calibration keep your equipment performing at peak, while built-in diagnostics help anticipate maintenance needs. And integrating robotic welding is now smoother than ever—whether for small batch flexibility or high-output cell automation.
Why Select Electronic Service Products for Your Laser Welding Solutions?
- Decades of experience delivering precision laser welding solutions
- Comprehensive support from consultation to production
- Fast quotes, transparent pricing, and turnkey project management
- In-house engineering to address demanding laser plastic welding and medical device applications
When every minute and every defect matters, trust Electronic Service Products (ESP) to deliver world-class laser welding solutions . With decades of experience in laser plastic welding , polymer welding , and metal applications, ESP’s experts guide you from initial assessment to final production. Whether you’re reshoring critical supply lines, launching new medical device assemblies, or integrating advanced welding systems on the shop floor, ESP offers the reliability and expertise that ensures results.
From rapid prototyping and small precision runs to scalable robotic welding solutions, ESP tailors each project for maximum impact. Benefit from expedited quotes, clear pricing, and full project management—plus in-house engineering that understands your regulatory, quality, and production challenges inside and out.
Key Takeaways: Maximizing Competitive Advantage with Laser Welding Solutions
- Laser welding solutions substantially improve output quality and reduce defects
- Onshore manufacturing limits tariff risks and accelerates delivery
- ESP delivers the flexibility, speed, and reliability modern supply chains require
Upgrading to laser welding solutions means gaining a real edge: reduced defects, faster time-to-market, and assurance of regulatory compliance. Onshoring your manufacturing not only limits economic risk but also empowers you to meet shifting market demands—and raise product standards. Partnering with ESP means plugging in expertise, agility, and a relentless commitment to your production goals.
Take Action Now to Reshore with Advanced Laser Welding Solutions
- Facing Tariff Pressures? It’s Time to Reshore Smarter. At Electronic Service Products, we specialize in precision laser machining solutions that meet the highest quality standards—onshore, on time, and on budget. Whether you're looking to reshore your manufacturing or avoid the mounting cost of overseas tariffs, we offer the speed, precision, and flexibility your supply chain demands. 👉 Call today 203-265-4167 or go to espcnc.com/request-a-quote
Ready to future-proof your production? Invest in laser welding solutions to boost output, reduce risks, and achieve quality onshore—where it matters most.
To further enhance your understanding of laser welding solutions, consider exploring the following authoritative resources:
-
“Laser Welding” : This comprehensive guide by IPG Photonics delves into the advantages of laser welding, including high precision, repeatability, and minimal maintenance requirements. ( ipgphotonics.com )
-
“ExactWeld - Automated Precision Laser Welding” : Coherent’s ExactWeld systems offer insights into automated precision welding for small metal parts, highlighting features like integrated scanners and user-friendly software. ( coherent.com )
These resources provide in-depth information on the benefits and applications of laser welding technologies, aiding in informed decision-making for your manufacturing needs.
Write A Comment