Why Precision Laser Technology is Reshaping the Manufacturing Landscape
Imagine trying to shape a complex part out of hardened material, facing sharp angles and demanding tight tolerances. Conventional machining can hit a wallâliterally and figurativelyâwhen asked to cut or drill such components with speed and accuracy. In todayâs era of fast-paced industrial development, manufacturers contend not only with the complexity of designs but also with the relentless demand for precision and durability. Many traditional methods fall short, resulting in compromised quality, wasted materials, and lost time. This is where 5-axis precision laser clean cutting, drilling, and welding steps in, providing solutions to challenges that once appeared insurmountable.
As industries push boundaries with advanced aerospace components, medical devices, and intricate electronics, the need for a technology that can maneuver through the toughest requirements becomes urgent. Not fully understanding or utilizing 5-axis laser solutions means exposing projects to inefficiencies, higher costs, and the real risk of falling behind competitors. For forward-thinking manufacturers, clarity on these methods is not just valuableâitâs essential for survival and advancement. Exploring how 5-axis precision laser clean cutting, drilling, and welding unlocks new possibilities will help you understand why this technology is quickly becoming a cornerstone of modern fabrication.
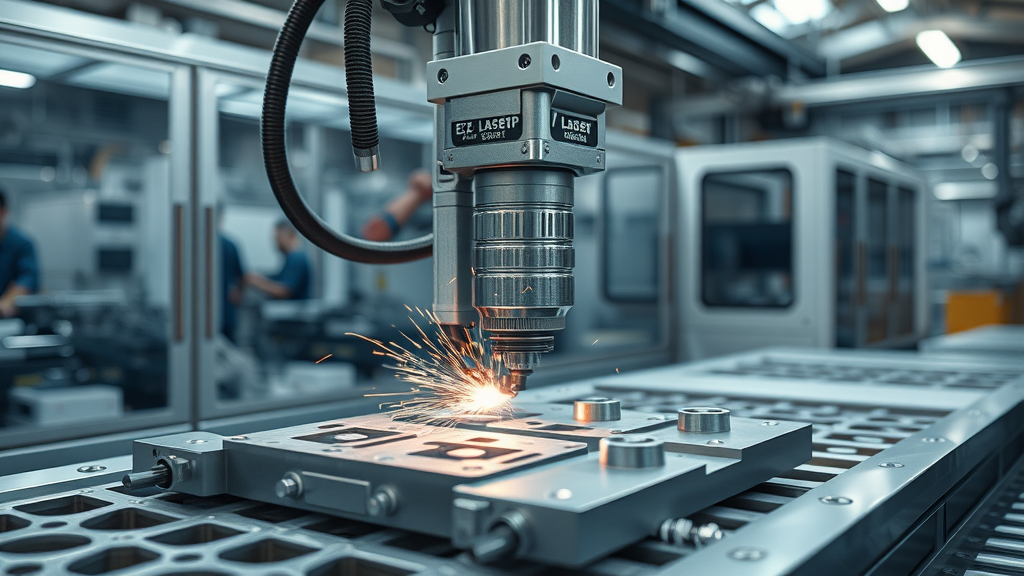
Unpacking 5-Axis Laser Clean Cutting, Drilling, and Welding: A Modern Engineering Marvel
At its core, 5-axis precision laser clean cutting involves harnessing computer-controlled lasers to make intricate cuts, drill minuscule holes, or weld with pinpoint accuracyâacross five axes of movement. This multidimensional freedom enables the laser to approach the workpiece from virtually any angle, making it possible to manufacture parts that feature complex geometries, curved surfaces, or hard-to-reach spots. The result? Consistent, high-quality finishes achieved faster and with significantly less material stress compared to methods constrained by rigid, linear movement.
By integrating clean laser cutting, drilling, and welding, manufacturers can address varied application demands using a single, unified technology. Tasks like cutting intricate shapes in challenging materials, drilling precise holes at odd angles, or joining dissimilar metals become not only feasible, but repeatable at scale. These advances reduce tooling pressuresâa major limitation in traditional methodsâwhile delivering tighter tolerances and refined finishes. Ignoring the potential of 5-axis laser technology means risking outdated production processes and missing out on dramatic gains in product quality and operational flexibility.
The Transformative Benefits of Advanced Laser Techniques in Real-World Manufacturing
Drawing on significant expertise in the field, Electronic Service Products demonstrates how the application of 5-axis precision laser clean cutting, drilling, and welding directly addresses critical manufacturing headaches. For example, clean cutting with lasers allows for the creation of complex parts at any angle, across diverse materials and thicknesses that would defy or damage traditional machining. This opens new avenues for designers and engineers to realize their visionsâno longer limited by the physical restrictions of conventional tools.
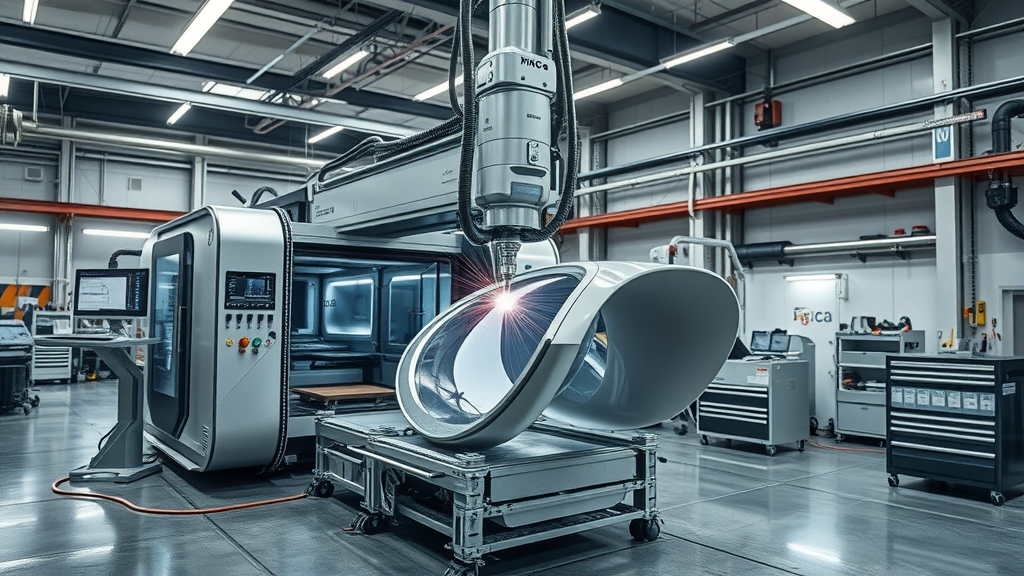
Laser drilling, another facet of the technology, becomes a crucial asset for parts that require complex entrance angles or where minimal tool pressure is vital. This precision enables the production of intricate, microscopic holes without the warping, stress, or distortion caused by mechanical methods. Laser welding, meanwhile, provides a means of joining metals and alloys with extraordinary precision, minimal heat input, and exceptional surface finishes. Such advantages not only improve the efficiency and speed of production but also enhance the lifespan and reliability of the final components, directly addressing priorities in industries that demand perfection.
From Prototyping to Production: How Flexibility Sets 5-Axis Laser Solutions Apart
The flexibility afforded by 5-axis laser systems is a decisive factor in their adoption. Unlike one-size-fits-all machinery, these laser solutions scale seamlessly between producing single-piece prototypes and high-volume production runs. With capacities to handle parts up to 46 inches in diameter, the technology supports manufacturers at every stageâfrom pilot projects requiring iterative refinement to full-scale output meeting the most stringent specifications. Versatility in material compatibility further broadens its application, covering metals, alloys, and other challenging substrates that might otherwise be problematic for conventional machining.
When edge quality, consistency, and turnaround are on the line, 5-axis systems offer something rare: the agility to switch seamlessly between jobs, ensuring deadlines and quality standards are met without compromise. This capacity to scale and adapt under pressure not only mitigates risk but also future-proofs operations against shifting customer demands or rapid changes in design requirements.
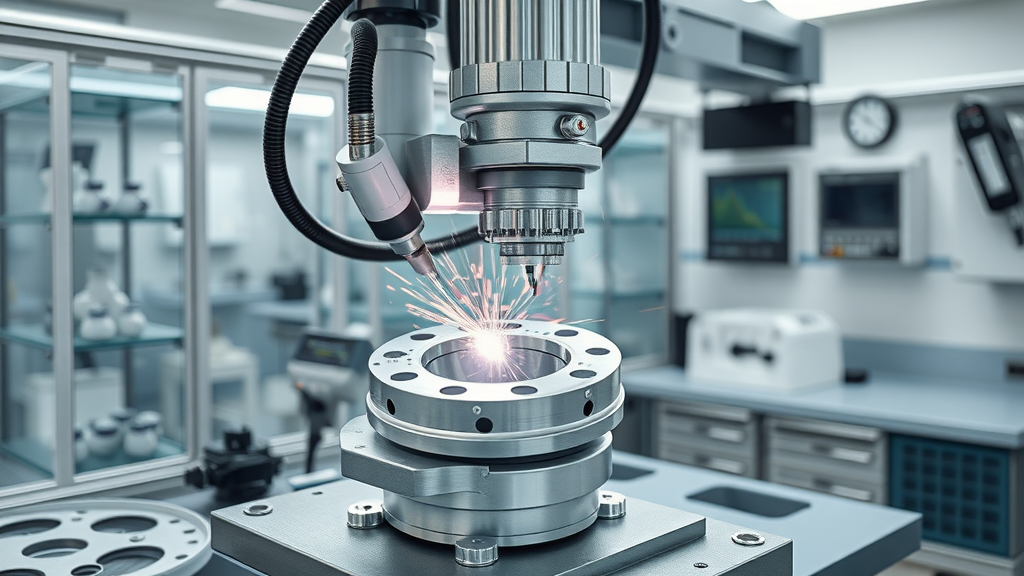
Precision, Reliability, and Finishes: Why Laser Methods Outperform Traditional Approaches
A defining characteristic of laser clean cutting, drilling, and welding is the precision delivered to every project. Components emerge with less distortion, superior edge quality, and near-perfect replication from the digital design to the physical workpiece. Compared to mechanical operations that can deform or stress sensitive materials, laser methods apply low heat and minimal contact, leading to little to no distortion and exceptional finishes straight off the machine. This reduces or eliminates the need for secondary processing, lowering costs and accelerating delivery timelines.
Reliability is further reinforced through rigorous maintenance and in-house expertise, a cornerstone visible in the day-to-day operations at experienced shops. Continuous uptime and a commitment to quality mean customers consistently receive products that meet or exceed their expectations, every single time.
Maintenance, Expertise, and the Pursuit of Continuous Improvement
The technical sophistication of 5-axis precision laser equipment demands regular care and expertise to maintain peak performance. Not all service providers approach this need with the same commitment. By integrating a dedicated repair and retrofit department, industry leaders are able to offer 24-7 maintenance and technical supportâan edge that translates into minimized downtime and reliable delivery schedules. Unlike shops that rely on third-party vendors for repairs, this focus on in-house proficiency is a strategic advantage, keeping the technology running smoothly and projects on track.
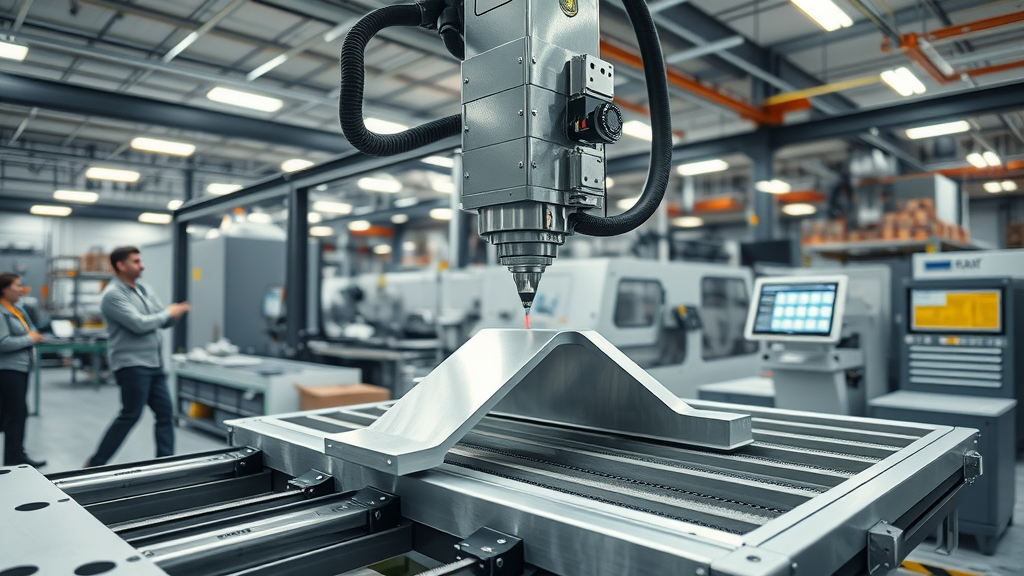
Long-term success in laser manufacturing hinges on an organizationâs willingness to embrace continuous improvement. Each job, whether a one-off prototype or a large production run, is subject to rigorous quality programs and the expectation that processes will evolve for ever-greater efficiency and precision. Such a philosophy ensures that customers benefit not only from advanced hardware, but also from a culture of ongoing progress.
Electronic Service Productsâ Commitment: A Perspective on Quality and Expertise in Laser Manufacturing
Electronic Service Products showcases a distinct approach rooted in a quality-first philosophy that permeates every step of the process. Their stated policyâto consistently provide products and services meeting or exceeding customer requirementsâplaces the focus on diligent workmanship and robust programmatic improvement. Employees are empowered to pursue excellence at each stage, delivering âright the first time and every time.â This mindset supports a culture where accountability and pride of craft are not aspirations, but everyday expectations.
With over sixteen years of dedicated experience and a comprehensive machine repair division, the organization embodies the high standards it sets. The ability to support both precision jobs and high-volume demands, combined with ongoing maintenance for laser platforms, underscores a deep commitment to reliability and the highest levels of customer satisfaction. This professional resolve is visible in their reputation for delivering on-time, in-spec partsâhallmarks of an industry authority rather than a mere vendor.
What Customers Experience When They Adopt Advanced Laser Solutions
When companies transition to 5-axis precision laser technologies, the difference is apparentâfrom reduced turnaround times to the flawless execution of intricate designs. While reviews are not currently listed for Electronic Service Products, the projected experiences highlight industry benchmarks: on-time delivery, specification adherence, and unwavering quality as products of commitment and expertise at every turn.
[Customer stories and feedback will reflect exceptional delivery, reliability, and the value of consistent precision achieved through advanced laser solutions.]
As more organizations step into the future of manufacturing, those who prioritize the integration of advanced laser techniques consistently enjoy improved efficiency and higher quality outcomes. By making forward-thinking choices today, manufacturers position themselves to capitalize on tomorrowâs opportunities.
How 5-Axis Precision Laser Clean Cutting Propels Industrial Progress
The rise of 5-axis precision laser clean cutting, drilling, and welding is a pivotal moment for manufacturers determined to stay at the forefront of their industry. This technology brings marked improvements in flexibility, accuracy, and production speedâqualities demanded by modern applications and customers alike. When practiced by organizations committed to ongoing advancement and impeccable quality, these capabilities shift from technical advantages to game-changing standards. As demonstrated by established leaders, the marriage of expertise and innovation sets a high bar in precision manufacturingâa standard that is increasingly becoming an expectation for customers and a necessity for future-ready operations.
Embracing 5-axis precision laser clean cutting not only transforms the quality of parts produced, but also ensures resilience and adaptability in the face of evolving challenges, placing companies ahead in the competitive landscape.
Contact the Experts at Electronic Service Products
If youâd like to learn more about how 5-axis precision laser clean cutting, drilling and welding could benefit your manufacturing process, contact the team at Electronic Service Products. đ Address: 126 S Turnpike Rd #2, Wallingford, CT 06492, USA đ Phone: +1 203-265-4167 đ Website: http://www.espcnc.com/
Electronic Service Products Location and Availability
đ Hours of Operation:đ Monday: 7:00âŻAMâââ3:30âŻPMđ Tuesday: 7:00âŻAMâââ3:30âŻPMđ Wednesday: 7:00âŻAMâââ3:30âŻPMđ Thursday: 7:00âŻAMâââ3:30âŻPMđ Friday: 7:00âŻAMâââ3:30âŻPMđ Saturday: â Closedđ Sunday: â Closed
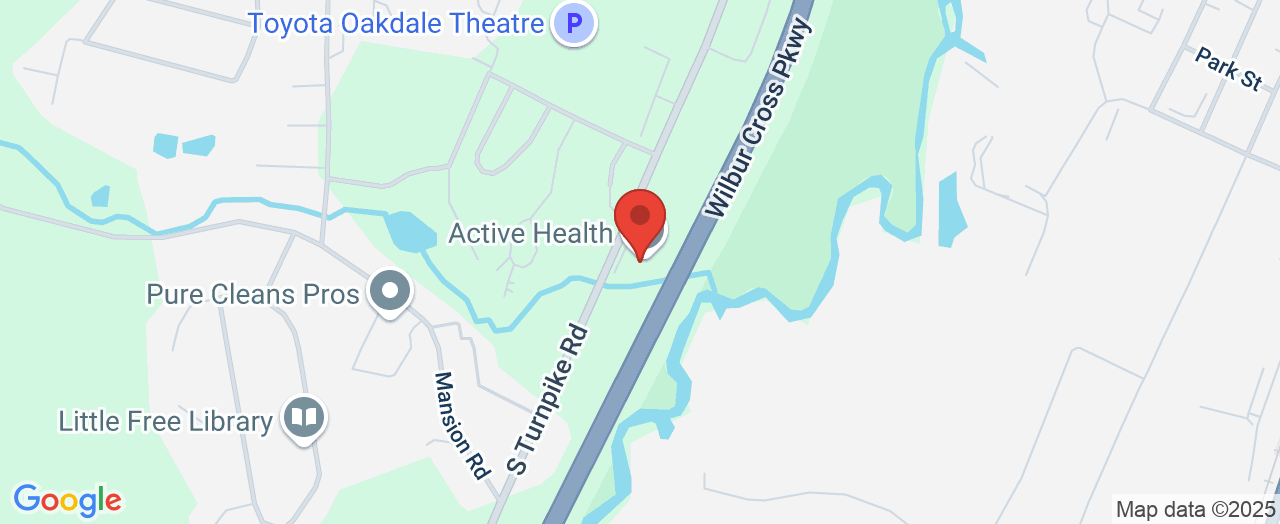
Write A Comment